Roughing in the turning operation refers to removing a substantial amount of excess material from a workpiece. It is the first step in the turning process. Furthermore, it produces shapes closely related to the required part geometry, making the process easier and more efficient.
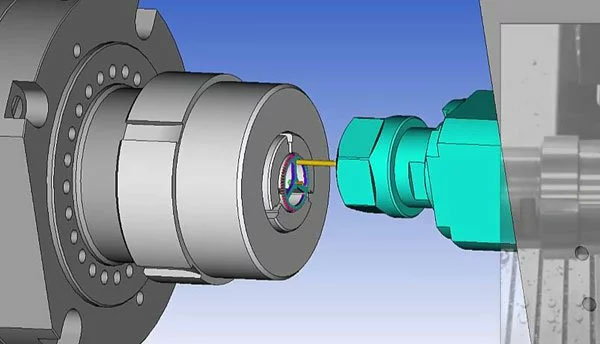
The benefit of roughing is that it removes empty allowances quickly, impacting product surface and dimension features. Although this operation enhances high productivity, it produces components that do not meet high accuracy.
Finish turning involves light removal from a workpiece material for surface finishing. It performs the final machining to achieve dimensional tolerances and surface finish. Tool wear out, built-up edges, and chip type can affect surface finish.
In addition, turning finishing is done to meet standard machining features in terms of flatness, roughness, thickness, and tolerance.
Here are the distinctive features of rough and finishing cuts for a better understanding:
Rough cutting requires a high material removal rate while finishing turning has a lower stock removal rate.
Finish turning has a good surface finish, while rough turning has poor surface quality.
Rough cuts have poor adherence to tight tolerance levels, while finish cuts have good adherence to tight tolerance.
Roughing has higher chip loads on the cutter while finishing has a lesser chip load.