CNC machining price may vary depending on different factors, as discussed below:
- CNC Machine Costs
Machining cost changes with the change of the type of machine. Mainly, there are two types of machines that are being used for manufacturing parts using CNC machining, i.e. 3 3-axis and multi-axis machines.
The machine cost is also dependent on various factors like the size & weight of the machine, speed, power, and machine configuration.
The machining cost is calculated per hour, and the approximate cost of 3-axis CNC machining is around 40$ per hour, while for CNC turning machines, it is about 35$ per hour. The hourly rate of CNC machining using multi-axis machines is comparatively higher, ranging between 75$ and 125$.
Due to the involvement of more complex parts, CNC milling is more expensive than other types of machining operations. The machining expenditures increase with the increase in axes of the milling machines. For example, in the case of 5-axis machining, it costs more as compared to 3-axis machines.
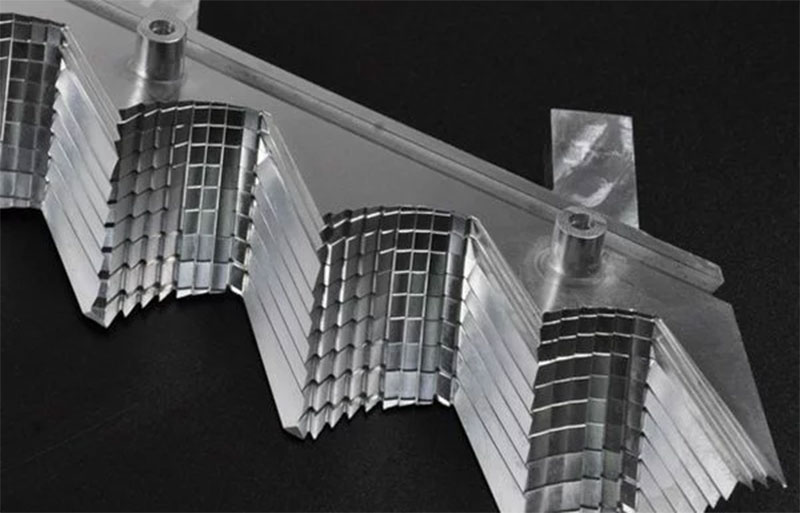
- Machining Time
The time required for the complete machining of any CNC machined part also plays a vital role in the calculation of the CNC machining cost. It is the rule of thumb that the more time taken for machining more the cost of the machining, which adds up to the basic setup cost.
Software like CAM, which requires a 3D CAD design model, can provide the estimation of the time required for the completion of the project. A project with a high level of complexity requires more hours to complete.
- Labor
One of the advantages of CNC machining, as compared to manual machining, is that it reduces the number of laborers that are involved in manufacturing. The primary cost of the labor is of the expert designer who designs the 3D CAD design model for the machining, which increases with the complexity of the desired product.
This cost remains the same even if you are required to manufacture more parts, which reduces the per-part machining price. Then, the additional cost is of the labor that operates the CNC machine, which also increases with the increased hours required for complete machining of the part.
The extra cost is added to the labor cost if manual work is done to assemble, finish, and post-process the parts. The extra labor cost is also added if the finished product is being delivered from the machine shop to the client at a different location.
- Material Costs
The material costs are also imperative in calculating the cost of CNC machining. The price of the final product made by a CNC machine depends on the type of materials from which you are required to make the product is made. You may be required to make part of plastic or metal materials.
As the plastic materials are cheaper and less durable, the machining cost of plastic or aluminum material is less compared to stainless steel. As in CNC machines, the material is removed from the solid blocks to make the 3D object. So, the required raw material will be more than the material of the final product.
The machinists buy the materials in the form of solid blocks and calculate the expense of the product per block. The most commonly used metals in CNC machining are aluminum, stainless steel, and brass.
Due to the economical prices and excellent machinability of aluminum, most machinists use aluminum in CNC machines.
Stainless Steel and brass result in higher costs due to poor machinability relative to aluminum. The titanium alloy is the most expensive of all these metals, so the machining cost of this metal will be the highest because it may require some special tools to manufacture the parts.
In case of the plastics, the price of the bulk material is less, the tools required also cost less, and less time is required to machine the plastics like Nylon, Delrin, and ABS.
- Surface Finish and Post-Processing
After machining, most parts come out with scratches and marks that may not be ideal for direct use at the time. This is where CNC machining surface finishes come in. This extra process will help conceal those unwanted marks and apply a protective coating to the part.
Although these post-processing activities are important, they usually attract extra costs. This process is totally separate from CNC machining and may even need extra tools and materials to be completed. Some of the common finishes include sanding, coating, anodizing, painting, chroming, blacking, galvanizing, brushing, and water transferring.
- Quantity
The volume of the order tremendously affects the cost of the final product. It is true that the overall cost will increase with the increase of required finished parts, but the cost per part will decrease. - Tooling Cost
In some cases of manufacturing, standard tooling is not useful, so custom tooling is required, which also increases the manufacturing cost using CNC machines. - Design Complexity
It can be difficult to reproduce some designs, especially when they have unique lines and shapes. Most times, manufacturers spend many hours programming and setting up the machine and cutting tools. This long process would certainly affect the final CNC machining price.
To achieve features like deep pockets and undercuts, you may also need to get special tools or multi-axis CNC machines, which leads to a higher cost. A simpler design with fewer tool changes and repositioning would always be more cost-effective than a detailed one.