Like all CNC machining devices, CNC routers interpret computer-generated designs and act upon them for precise cutting and shaping. All CNC operations begin with the engineers creating the design using CAD software, which could be in the form of a 2D drawing or a 3D model.
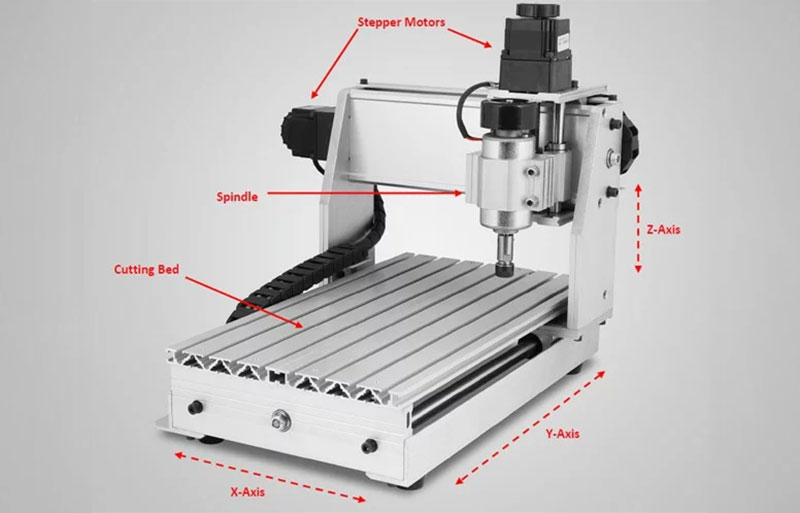
Then, the CAD file is converted into a CAM file, which entails the tool paths and other parameters, such as depth of cutting, feed rates and cutting speed, which the CNC routers will follow to work.
Afterward, the machinist uploads the CAM file to the CNC router’s control software and then sets up the material on the router’s worktable, securing it to prevent movement during cutting.
The following action configures the machine parameters to ensure the device precisely and accurately cuts the material to suit the intended specification. Once this is set, the CNC router is activated and follows the programmed toolpaths as it machines the material to fit the desired outcome.