With so many types of milling operations to choose from, making the optimal choice can be a challenging task. Generally, there are several factors that engineers must consider when selecting milling operations for their manufacturing plans.
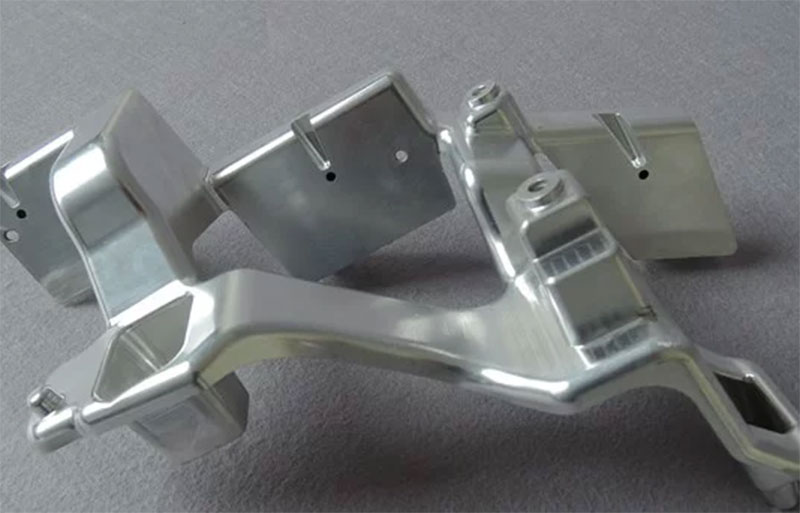
Part Geometry
The geometric features of the part are the first thing to look at when selecting milling processes for a part. Specific features like angled surfaces, curvature, and threads can help shortlist the milling process to a manageable number.
For instance, an automotive panel, owing to its complex curvature, would most certainly require advanced milling techniques like profile milling with a CNC milling machine.
Machine Tool Capability
Different milling machines have different machining capabilities. A manual milling 3-axis machine is perfect for simple jobs like squaring stocks, cutting angled surfaces, or producing planar surfaces. A more complex operation, like profile milling, however, may not be possible without a multi-axis CNC milling machine.
Similarly, a turn-mill center is a specialized machine tool that can efficiently produce primarily cylindrical parts with prismatic features.
Quality Requirements
Quality requirements like surface finish and tolerances also dictate the choice of the milling process. Climb milling, for example, would be more suitable if high-quality production is desired. A CNC milling machine is the preferred choice if tight tolerances are required.