If the demand for many plastic parts is not high or the mold opening cost is high, silicone molds can be used to manufacture them. These molds are made of silicone materials, with low manufacturing costs and short cycles. Below, we will explain the manufacturing method of rapid tooling to everyone.
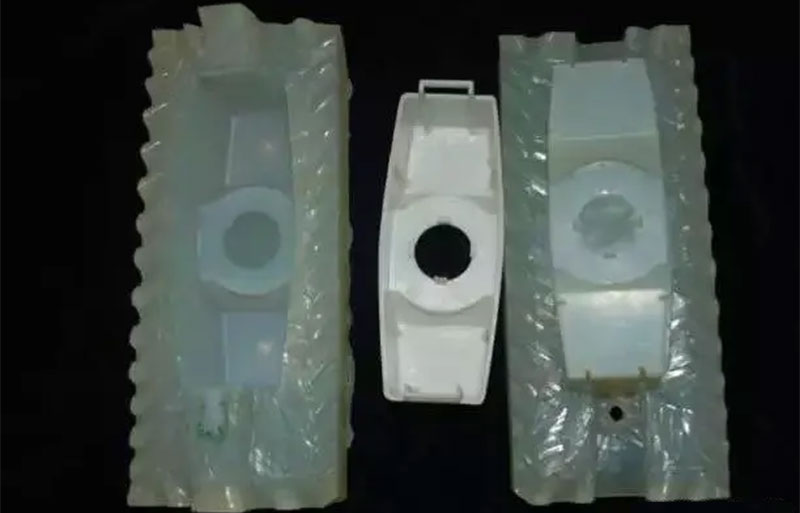
Step 1: First, use 3D printing or CNC to create a workpiece that you want to make, which is also known as creating a prototype. For example, in the communication phone shown in the picture, if you want to make 100 or 200, you need to first create a prototype and then use it to make a mold.
Step 2: Analyze the prototype and determine how to easily pour and mold the water outlet. Then, select a suitable box based on the size of the prototype to make a silicone container. When placing the prototype inside, ensure that there is a distance of about 20mm between the prototype and the box.
Step 3: Mix the silicone liquid and silicone curing agent in proportion and stir evenly until they are as high as a box. The silicone liquid should cover the prototype by more than 30mm.
Step 4: Vacuum the box of poured silicone liquid, as there will be a steam drum in the poured silicone. Only by removing the thick silicone from the steam drum can it become a solid filling. Then let it stand for 1-2 hours until the silicone liquid becomes solid, cut open the silicone and take out the prototype, which becomes the mold.
Step 5: Close the mold and tie it tightly with sealing tape to pour the product.
Is it easy? Note that this type rapid tooling is very different from injection molding, with different materials and molding methods. It can be used to cast ABS, PC, PP, PMMA, soft rubber, POM, and so on.