To increase the number of mold uses for liquid silicone rubber molds, one can approach the issue from the following aspects:
I. Selection of Suitable Liquid Silicone Material
Quality Silicone Choice: Choosing high-quality liquid silicone is crucial for increasing the number of mold uses. High-quality silicone materials typically exhibit better resistance to aging, high temperatures, and tearing, allowing them to withstand more molding operations without easy damage.
Balancing Hardness and Toughness: The hardness of the silicone should be moderate, generally between 20~30 Shore A, which ensures sufficient toughness while reducing bubble formation and enhancing mold durability. Meanwhile, it is important to avoid selecting silicone with too low hardness to prevent insufficient tear and tensile resistance.
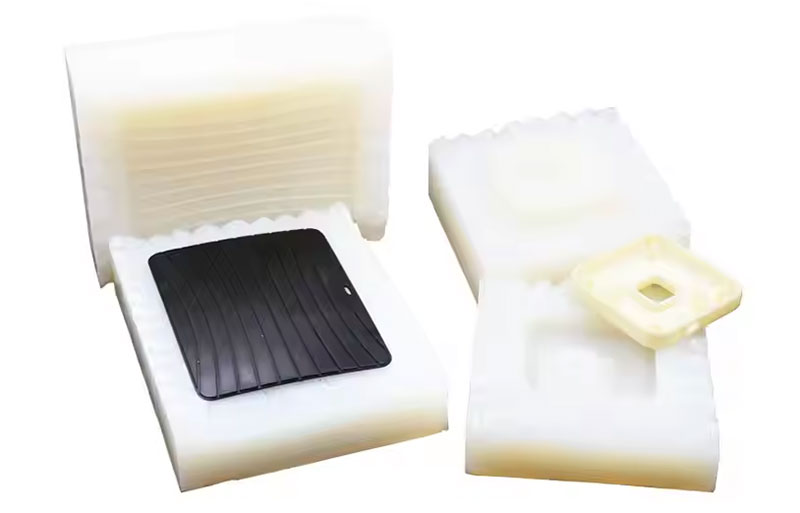
II. Proper Production and Use of Silicone Molds
Proportional Mixing: Strictly follow the proportions provided by the manufacturer to mix silicone and curing agent, ensuring uniform mixing. Uneven mixing can lead to uneven curing of the mold, affecting its lifespan.
Vacuum Degassing: During production, perform vacuum degassing on the silicone to eliminate bubbles, improving the mold’s compactness and durability.
Application of Mold Release Agent: Apply an appropriate amount of mold release agent before using the mold to facilitate mold release and reduce mold wear. Choose the right type of mold release agent to suit different molding materials.
Avoid High Temperatures and Fire Sources: Silicone molds should be kept away from high-temperature fire sources and power sources to prevent accelerated aging. If baking is required, it should be done in an oven with controlled temperatures.
III. Enhancing Mold Structure
Adding Reinforcing Materials: When producing large or complex molds, reinforcing materials such as fiber cloth or glass fiber cloth can be added to the silicone to improve the mold’s tear resistance and lifespan.
Rational Design of Mold Structure: Optimize the mold’s structural design, such as adding reinforcing ribs or changing the mold’s wall thickness, to enhance the mold’s overall strength and stability.
IV. Proper Maintenance and Care
Regular Cleaning: Promptly clean the mold surface of residues after use to avoid corrosion and damage. Avoid using corrosive reagents and hard tools during cleaning.
Proper Storage: Store the mold in a dry, dust-free environment, avoiding direct sunlight and heavy compression. Regularly inspect and maintain molds that are not in use for an extended period.
Rotational Use: If multiple molds are available, it is recommended to rotate their use to distribute wear and avoid excessive use of a single mold, leading to damage.
V. Other Considerations
Understanding Material Properties: Before production, fully understand the properties of the molding material to select the appropriate silicone type and ratio.
Controlling Curing Time: For molding materials that require curing, strictly control the curing time to prevent silicone molds from aging due to prolonged heat exposure.
Following Operational Norms: Strictly adhere to operational norms during molding operations to avoid mold damage due to improper handling.
In summary, by selecting suitable silicone materials, properly producing and using silicone molds, enhancing mold structure, properly maintaining and caring for them, and following operational norms, the number of mold uses and lifespan of liquid silicone rubber molds can be effectively increased.